Both terms “quartzite” and “quartz” sound alike. People who are not stone experts fail to sort out the difference between the two stone types. Both stone types are quite different from each other in terms of features and output. Quartz is a manmade stone product. On the other hand, quartzite stone comes from quartzite quarries. The quartz, found in clusters naturally, is not suitable for various slab applications in residential and commercial construction projects. For effective use in various projects, quartz materials must be converted into engineered stone. It is the right mix of pigments, additives, quartz aggregate chips, and unsaturated polyester that helps in making functional and ready-to-use engineered stone slabs and countertops. This content puts light on the process of making engineered quartz and materials used to form functional quartz products.
Raw Materials Needed For Manufacturing Engineered Quartz Slabs
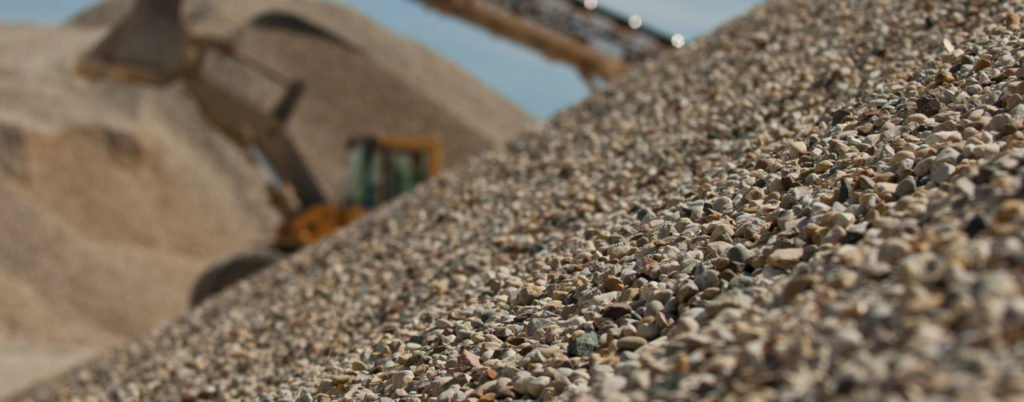
In the modern world, there is no dearth of engineered quartz slabs in the competitive market that is global. In many colors, patterns, and texture range, quartz slabs are durable and non-porous. To cater to the growing needs of domestic and commercial construction, quartz companies produce a variety of slab products. For making engineered quartz slabs, quartz engineers need various raw materials available around in bulk. These raw materials include:
Based on physical and mechanical properties, calcareous and siliceous aggregates are chosen in the form of sand or grain. These aggregates are mixed with binding agents to create a compact stone mix.
Aggregates
Based on physical and mechanical properties, calcareous and siliceous aggregates are chosen in the form of sand or grain. These aggregates are mixed with binding agents to create a compact stone mix.
- Siliceous aggregates – Basalt, quartzite, quartz, granite, porphyry, and silica sand
- Calcareous aggregates – Dolomite, marble, or colored stones
Mineral Fillers
Mineral fillers are finely-pulverized stone materials that quartz engineers mix with resin to make bonding agents. Note that mineral fillers are easily available raw materials.
Bonding Agents And Additives
When stone experts talk about bonding agents, they indicate organic resins (unsaturated polyester resins). The additives used in the aggregate mix are accelerators and catalysts that harden the bifunctional silanes and resin.
Coloring Agents
The coloring agents are metal oxide pigments that have an important role to play in the process of stone mixing. Coloring agents are vital for rendering unlimited choices in the appearance of quartz slabs.
Add engineered quartz stone image (use any stockyard image)
The Manufacturing Process Of Engineered Quartz
Once quartz manufacturers stock different raw materials, they start the process of slab making as per the changing needs of B2B buyers. The process of manufacturing engineered quartz stone includes the following steps:
- 1 The selection of crushed raw quartz materials.
- 2 Mixing of raw quartz materials in the ratio of 93%:7%.
- 3 The ratio includes 93% quartz aggregates and 7% polyester resin plus other additives.
- 4 A vacuum and vibration process helps in compacting the mixture into slabs.
- 5 The vacuum functions in 100 seconds at a pressure of about 100 tons.
- 6 This process reduces water absorption and minimizes porosity.
- 7 Curing of slabs in a kiln at 85-degree temperature for at least half an hour.
- 8 The slab curing process helps in gaining stain resistance properties
- 9 Ovens and steams can help in accelerating the curing process.
- 10 Finally, the process of slab calibration, gauging, polishing, and packing takes place.
Technical Characteristics Of Engineered Quartz
Like natural stone products, a quartz slab also comes with lots of physical and chemical properties that make the slab stone fit for end-use. Generally, the ratio of raw quartz materials can be reduced or increased by slab manufacturers as per their stone making patterns. The following is a brief detail of engineered quartz stone characteristics that are common in a large number of quartz slabs. It includes:
- Density – 2.4 to 2.5 g/cm3
- Water Absorption – 0.01-0.2%
- Modulus of Rupture – 41-58 Mpa
- Compressive Strength – 150-240 Mpa
- Abrasion Resistance – 58-63 (Index)
- Hardness – 6-7 Mohs
- Acid Resistance – Yes (certain extent)
Quartz buyers looking for a bulk order can also ask quartz manufacturers to make customized slab sizes as per the need of their B2C buyers. There are lots of engineered quartz options available for B2B buyers in the Indian stone market. Like the natural stone industry, India also enjoys the status of a growing engineered quartz hub. The hub is known for both engineered quartz manufacturing and export. Moreover, the production capacity of quartz slab plants is also higher. That is the prime reason why this hub entices a large number of buyers from all corners of the world. This hub ensures buyers a plethora of colorful and patterned choices.